Embedded systems are everywhere. They are specialized computing systems, designed with precision to perform specific tasks reliably and efficiently, often in real-time environments where there’s no room for error. Unlike general-purpose computers like PCs or smartphones, which handle a variety of tasks simultaneously, embedded systems are tailored to excel at a single function. Think of the Anti-lock Braking System (ABS) in your car that prevents wheel lock-up during sudden braking, or the microprocessor in your smartwatch that monitors your heart rate. These systems are crucial for their ability to make quick decisions that keep us safe and ensure our devices work smoothly.
Why automated testing of embedded systems matters
Given the vital roles embedded systems play, it’s essential to ensure they work flawlessly in all situations. This is where test automation becomes indispensable. Unlike manual testing, which can be slow and error-prone, automated testing offers continuous and systematic checks on embedded systems. These tools simulate real-world scenarios, allowing developers to catch and fix issues early in the software development process, well before they can cause problems for users.
As embedded systems become more complex and are used in more safety-critical applications—like medical devices, autonomous vehicles, and industrial automation—the need for rigorous software testing grows. Automated testing ensures these systems not only perform their intended functions but also maintain reliability over time. It helps developers save time and money by catching bugs early, reducing the risk of costly fixes later on.
In environments where embedded systems must run continuously, automated testing provides the confidence that these systems can handle long-term operation without degrading in performance. This reliability is crucial in fields like healthcare, where the failure of an embedded system could have life-threatening consequences.
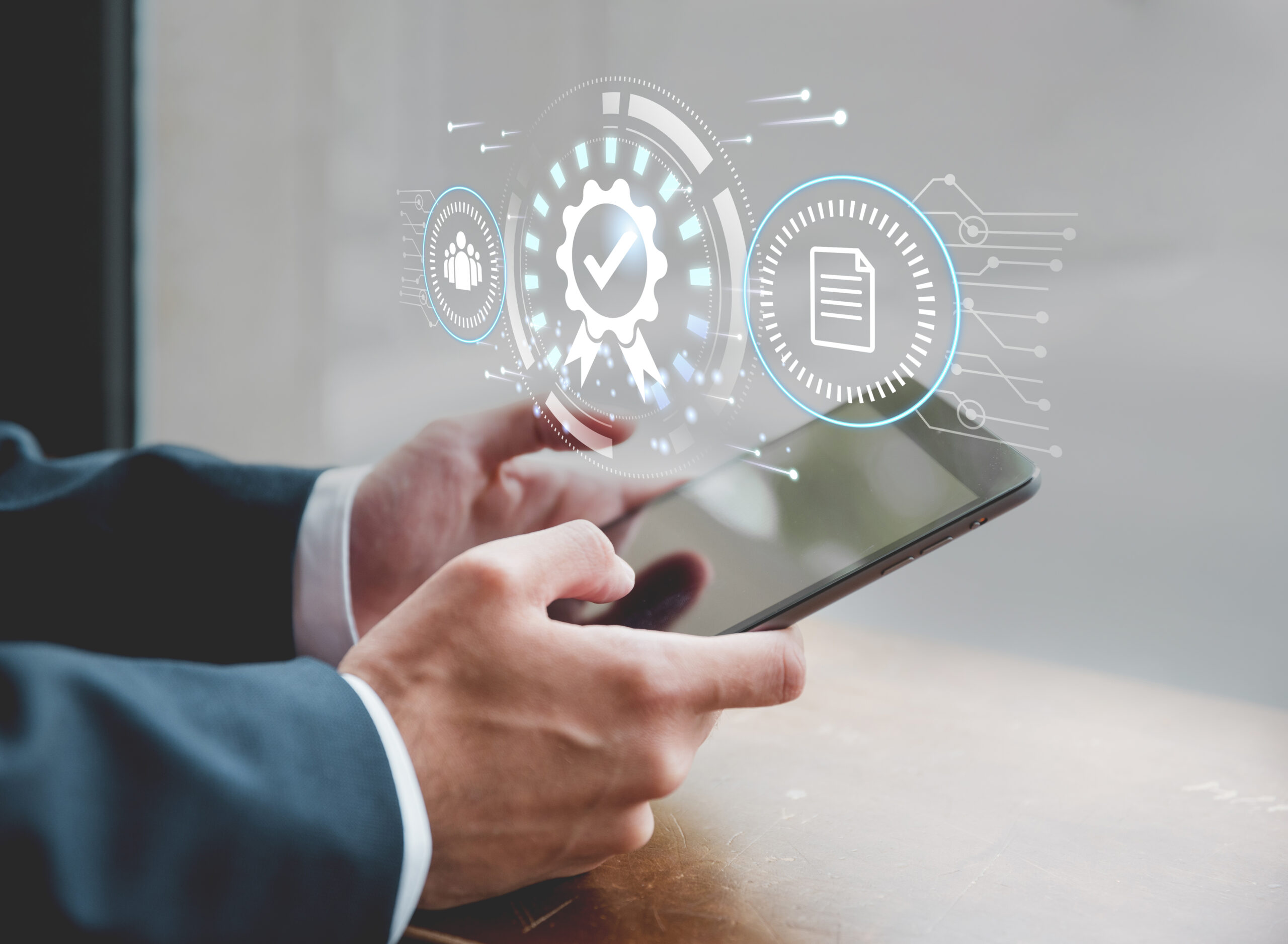
Table of Contents
What Are Embedded Systems?
Getting to the Basics
An embedded system is a sophisticated integration of hardware and embedded software, meticulously designed to perform a specific task with precision and efficiency. At the heart of an embedded system, you’ll typically find a microcontroller or microprocessor—acting as the “brain” of the operation—responsible for executing commands and managing tasks. This central processing unit (CPU) is supported by various components, including memory for data storage, input/output interfaces for interaction with the external environment, and firmware, which is the specialized software that directs the hardware’s actions. Unlike general-purpose computers, which can run multiple applications, embedded systems are built to perform dedicated functions, often under strict time constraints.
A key element in many embedded systems is the real-time operating system (RTOS). The RTOS ensures that all processes are carried out in a timely manner, minimizing latency and guaranteeing that the system can respond to inputs almost instantaneously. This is crucial for applications where timing is everything—such as in automotive safety systems or industrial automation, where even a slight delay could have significant consequences.
Real-World Examples You Know
Embedded systems are integral to many devices that we rely on daily, often operating behind the scenes to ensure smooth functionality. For instance, consider the pacemaker—a compact, life-sustaining device implanted in patients to monitor and regulate heartbeats. The embedded system within the pacemaker continuously processes data, making real-time adjustments to the heart’s rhythm as needed. Another familiar example is the smartwatch, which goes beyond telling time to monitor your physical activity, sleep patterns, and even deliver notifications—all thanks to the embedded systems working inside. These examples highlight the versatility and critical importance of embedded systems in both medical technology and consumer electronics.
Beyond these, embedded systems are also found in more extensive applications, such as in industrial machinery, where they control processes like assembly line operations, or in telecommunications, where they manage data routing and signal processing. These systems are often designed for reliability and durability, able to function in harsh environments and under demanding conditions.
Technical Aspects of Embedded Systems
Embedded systems can vary widely in complexity and capability, from simple microcontrollers controlling a single function to more complex systems managing multiple tasks simultaneously. For example, a Raspberry Pi, though often used in educational projects and hobbyist applications, can be considered an embedded system depending on its use. While the Raspberry Pi is technically a single-board computer capable of running a full operating system like Linux, it is frequently employed as the central controller in embedded systems for specific applications, such as home automation or IoT devices.
In contrast, simpler embedded systems might use microcontrollers like the Arduino, which are designed to perform more specific, limited tasks with minimal hardware resources. These microcontrollers typically include onboard memory, a small CPU, and limited input/output options, making them ideal for controlling sensors, motors, or other peripherals in real-time environments. This hardware, paired with the firmware, enables the system to perform its designated function efficiently and reliably.
Unique Features
Embedded systems possess several distinctive characteristics that set them apart from general-purpose computing systems. First and foremost, they are often designed for real-time operations, meaning that their responsiveness must be almost immediate. For example, in an automotive application like an airbag system, the embedded system must detect a collision and deploy the airbag within milliseconds to protect the occupants. The ability to perform such time-sensitive tasks makes real-time performance a critical feature of embedded systems.
Another defining characteristic of embedded systems is their resource-constrained nature. Unlike general-purpose computers, embedded systems are typically designed to operate with limited processing power, memory, and energy consumption. This makes them highly efficient, yet challenging to design and optimize. For instance, in battery-operated devices like pacemakers or wearable technology, the embedded system must function effectively for long periods on minimal power, making energy efficiency a top priority. Additionally, embedded systems are often built to be highly reliable, capable of functioning continuously for extended periods without failure, which is crucial in applications like industrial control systems or medical devices.
Furthermore, embedded systems are often developed with specific security testing features to protect against potential threats, especially as these systems become more interconnected through IoT (Internet of Things) networks. Security testing protocols are integrated into the design to safeguard sensitive data and ensure the system’s integrity, which is particularly important in applications like healthcare and finance.
Enhancing Safety with Automated Testing
Given the critical roles that embedded systems play in various sectors, ensuring their reliability and safety is paramount. Automated testing plays a crucial role in this by continuously and systematically validating the system’s performance. By catching potential issues early in the development process, automated testing helps to prevent failures that could have serious consequences, particularly in safety-critical environments like healthcare and automotive systems.
The Critical Role of Automated Testing in Embedded Systems
Ensuring Consistent Reliability
In embedded systems, reliability is not merely desirable—it’s essential. These systems often control critical functions where even the slightest failure can lead to severe consequences. Automated testing is a cornerstone in guaranteeing that these systems perform consistently and accurately, regardless of the application. Whether you’re dealing with a Raspberry Pi-based monitoring system or an Arduino-driven automation setup, automated testing provides the rigorous verification needed to ensure that the system functions reliably from development through deployment. By systematically identifying potential issues early, automated testing helps prevent failures and ensures that these systems meet the high standards required for their intended applications.
Expanding Testing Scope and Maintaining Precision
One of the most significant advantages of automated testing is its ability to comprehensively test a wide array of scenarios, far beyond what manual testing can achieve. Automated tools can simulate a broad range of conditions, including those rare edge cases that are often challenging to replicate manually. For instance, in a Raspberry Pi project managing environmental controls, automated tests can simulate varying conditions to ensure the system responds correctly under all circumstances. This thorough coverage is essential for verifying that the system will perform reliably in real-world conditions.
Automated testing also ensures consistency across multiple test runs, something manual testing can struggle with due to human error. Automated tests execute the same procedures with precision every time, providing reliable and repeatable results. This consistency is crucial for embedded systems that must maintain high reliability over long periods, such as an Arduino-controlled device that needs to perform accurately after numerous operational cycles.
Enhancing Efficiency and Early Issue Detection
Automated testing is not only thorough but also highly efficient. It enables continuous testing of embedded systems, running tests around the clock and identifying issues early in the development process. This early detection of defects is especially valuable in systems like those built on Raspberry Pi or Arduino, where rapid prototyping and iterative development are common practices. By catching issues early, automated testing helps avoid costly fixes later in the development cycle, significantly reducing both time and expenses.
In a practical application, automated testing in a Raspberry Pi-based network security project could continuously monitor system integrity and performance, quickly identifying vulnerabilities or malfunctions. This continuous testing aligns well with modern development methodologies like continuous integration and continuous delivery (CI/CD), where maintaining a steady and rapid development pace is critical.
Comprehensive Testing Strategies for Embedded Systems
Unit Testing: Ensuring Core Component Integrity
Unit testing is the foundation of any robust testing strategy, focusing on verifying the functionality of individual components or “units” within the embedded system. For platforms like Raspberry Pi or Arduino, unit testing might involve checking specific modules, such as sensors or controllers, to ensure they operate correctly in isolation. For example, automated unit tests on a Raspberry Pi could verify that GPIO pins are correctly controlling devices like LEDs or motors. Tools such as pytest or unittest in Python can be integrated with Raspberry Pi to automate these tests, providing immediate feedback and ensuring that each component performs as expected.
Integration Testing: Validating Inter-Module Communication
After individual components have been validated, integration testing ensures that these components work together seamlessly. In a Raspberry Pi-based system, integration testing might involve ensuring that sensors communicate effectively with the central processing unit and that the system accurately triggers actions based on sensor data. Similarly, for an Arduino project, integration testing would verify that all hardware components, such as motors, sensors, and controllers, interact smoothly without conflicts. Tools like Jenkins or Travis CI can automate these integration tests, ensuring that all parts of the system function together as intended.
System Testing: Assessing the Entire System in Real-World Conditions
System testing evaluates the entire embedded system as an integrated whole, ensuring that all components and subsystems work together under real-world conditions. For instance, if a Raspberry Pi is used in a weather station, system testing would validate the entire setup, including data collection from sensors, data processing, and output display, under various simulated weather conditions. Automated system tests can mimic real-world scenarios, such as power fluctuations or extreme environmental conditions, to ensure the system remains operational. In industrial applications, system testing might involve subjecting an Arduino-based control system to varying load conditions, verifying that the system can handle stresses like electrical noise or temperature changes.
Regression Testing: Ensuring Stability Through Continuous Updates
Regression testing is essential whenever updates or modifications are made to the system. This type of testing ensures that new changes do not introduce new issues or disrupt existing functionality. In embedded testing specifically the systems where updates can involve firmware changes, hardware modifications, or software enhancements, regression testing is critical for maintaining system stability. For example, after updating the firmware on a Raspberry Pi-based IoT device, regression testing would verify that all previously working features continue to function correctly. Similarly, in Arduino projects, regression tests ensure that updates to control algorithms or sensor inputs do not negatively impact system performance. Automated regression testing tools can be configured to run these tests automatically whenever changes are made to the source code, helping maintain the system’s reliability over time.
Challenges and Limitations in Embedded System Testing
Navigating Hardware Constraints
Testing embedded systems can be particularly challenging due to inherent hardware limitations. Many embedded devices operate with minimal processing power, limited memory, and constrained energy resources, making comprehensive testing difficult. For instance, when testing a battery-operated wearable health monitor, it’s crucial to avoid draining the battery or overloading the processor. This requires testers to carefully balance the need for thorough testing with the hardware’s constraints, often necessitating optimized test cases and external simulators to ensure thorough validation without overwhelming the system.
These hardware limitations also mean that certain types of tests, such as extensive performance evaluations, might be restricted due to the device’s capacity. Testers must therefore design tailored approaches that focus on critical areas while acknowledging these constraints, ensuring that essential features are rigorously validated without compromising the device’s operational integrity.
Addressing Real-Time Constraints
Embedded systems often function in real-time environments, where they must respond to inputs within tight timeframes. For instance, in a drone’s flight control system, the software must process sensor data and adjust the flight path within milliseconds to maintain stability and avoid obstacles. Testing such real-time systems involves not only validating functionality but also ensuring that the system meets strict timing requirements consistently.
Automated tests for real-time systems must be designed to evaluate performance under various conditions, ensuring the system can consistently meet timing constraints. This could involve testing under different load conditions or simulating delays to verify the system’s response times. Ensuring correct timing and synchronization is critical for real-world applications.
Managing Complex System Integration
As embedded systems grow more sophisticated, integrating multiple components becomes increasingly complex. This complexity is particularly pronounced in industries like telecommunications, where numerous systems must interact seamlessly to ensure reliable data transmission and processing. For example, in a satellite communication system, various subsystems—including signal processing, data encryption, and transmission modules—must work together flawlessly. Testing these integrated components is essential, as any failure in their interaction could lead to significant communication disruptions.
Automation is invaluable in managing this complexity by enabling thorough testing of interactions between different components. For instance, automated testing in a smart city traffic management system might involve verifying that sensors, data processing units, and traffic control mechanisms interact correctly to manage traffic flow efficiently. Comprehensive automated testing ensures that all components work together as intended, reducing the risk of integration failures that could have serious consequences.
Best Practices for Effective Automated Testing in Embedded Systems
Initiating Testing Early
A key strategy for ensuring the reliability of embedded systems is to begin automated testing early in the development process. By integrating testing from the outset, potential issues can be identified and addressed before they escalate. For example, in developing a smart agriculture system, incorporating automated tests within a continuous integration pipeline ensures that each code change is immediately tested, allowing developers to catch and fix errors quickly. This proactive approach helps maintain high quality throughout the development lifecycle and minimizes the risk of costly defects later on. Furthermore, tests can be grouped into a comprehensive test suite that ensures all critical aspects of the system are thoroughly verified.
Adopting a Modular Testing Approach
Focusing on individual modules before integrating them into the broader system is a prudent strategy. By isolating and thoroughly testing each module—such as a humidity sensor in a smart irrigation system—developers can ensure that each component functions correctly before it interacts with other parts of the system. This modular approach simplifies troubleshooting and helps prevent integration issues, ensuring that problems are identified and resolved at the earliest stage possible.
Utilizing Mocks and Stubs for Isolated Testing
Mocks and stubs are essential tools for testing components in isolation, especially when other parts of the system are still in development. These tools simulate the behavior of other system components, allowing you to test specific units without needing the entire system to be functional. For example, in developing an autonomous robot, mock sensors can be used to simulate environmental inputs, ensuring that the robot’s control system responds correctly even when the actual sensors are not yet available. This approach accelerates the testing process and helps identify issues early.
Automating Regression Testing to Maintain Stability
Regularly running regression tests is crucial to maintaining the stability of embedded systems, particularly after updates or modifications. In systems like automated manufacturing equipment, where a malfunction could halt production lines, automated regression testing ensures that new updates do not introduce new issues. By automating these tests, you can quickly verify that the system’s existing functionality remains intact, even as new features or updates are implemented. This continuous validation helps maintain system reliability over time and reduces the risk of unexpected failures.
Designing Realistic and Robust Test Scenarios
Effective testing must closely simulate real-world conditions to ensure that the system performs reliably under all expected circumstances. For instance, when testing a smart energy management system, it’s important to simulate varying power loads and usage patterns to verify that the system can manage energy distribution effectively. By designing test cases that reflect real-world usage scenarios, you ensure that the embedded system will perform reliably once deployed, providing confidence that it can handle the challenges it may face in actual operation.
Tools for Automated Testing in Embedded Systems
When it comes to setting up automated testing for embedded systems, choosing the right tools can make all the difference. Here’s a rundown of some tools that can help you get the job done effectively:
Unit Testing Frameworks
If you’re working with embedded systems, you’ll often need to verify that individual components, like sensors or controllers, are working correctly on their own. Tools like CppUnit or Unity are specifically designed for C/C++ applications, which are commonly used in embedded systems. They help you automate these tests, making sure each part of your system does exactly what it’s supposed to before you start integrating everything together. Google Test is another popular option, offering a flexible way to write and run tests, particularly if you’re dealing with more complex C++ code.
Hardware-In-the-Loop (HIL) Testing Tools
For more complex systems that need to interact with real-world hardware, HIL testing tools like dSPACE and NI VeriStand are invaluable. These tools let you connect your embedded system to either real or simulated hardware, so you can see how it behaves in a controlled environment. Whether you’re testing how a controller responds to sensor inputs or how a communication module handles data traffic, HIL testing gives you a clear picture of how your system will perform once it’s out in the field.
Continuous Integration Tools
To keep things running smoothly as your project evolves, continuous integration (CI) tools like Jenkins, GitLab CI/CD, or Travis CI are a must. These tools automatically run your tests every time you make changes to the code, catching any issues before they can snowball into bigger problems. This is especially useful in embedded systems, where frequent updates are common and any new bug could potentially cause serious issues down the line.
Simulation Tools
If you’re still in the early stages of development or you want to test your system without needing the actual hardware, simulation tools like QEMU or Proteus can be a lifesaver. These tools let you create a virtual version of your embedded environment, including the processor and peripherals, so you can run your tests without any physical setup. It’s a great way to test your code in a safe environment before moving on to real-world testing.
Code Coverage Tools
To make sure your testing is thorough, code coverage tools like gcov and LCOV can help you see how much of your code is being tested. High coverage means that most of your code has been run through tests, which is crucial for ensuring that every part of your system works as it should, especially in critical applications.
By carefully selecting and using these tools, you can build an automated testing setup that not only catches bugs early but also ensures your embedded system is robust, reliable, and ready for the challenges of the real world.
How T-Plan Can Help
At T-Plan, we understand the unique challenges involved in testing embedded systems, from ensuring real-time performance to managing hardware constraints. Our comprehensive testing solutions are designed to meet these challenges head-on, providing robust tools that cover every aspect of embedded system testing—from functionality to performance, integration, and security.
T-Plan Robot offers a versatile platform that integrates seamlessly with your CI/CD pipelines, allowing for continuous and automated testing of embedded systems throughout the development lifecycle. With T-Plan, you can automate regression testing, ensuring that any updates or changes don’t disrupt existing functionality. Our solution supports Hardware-In-the-Loop (HIL) testing, allowing you to simulate real-world conditions and validate your system’s interactions with hardware components. Additionally, T-Plan’s powerful scripting capabilities enable you to create detailed test scenarios that mimic real-world conditions, ensuring that your system is rigorously tested under a variety of scenarios.
What sets T-Plan apart is its flexibility and ease of integration. Whether you’re working with microcontrollers, complex IoT devices, or large-scale industrial systems, T-Plan provides the tools you need to automate testing effectively. Our platform is designed to handle the complexities of embedded system testing, offering a scalable solution that grows with your project’s needs.
Ready to Get Started?
If you’re committed to achieving excellence in your embedded system testing, T-Plan is the ideal partner to help you get there. Our automated testing solutions are built to enhance the reliability, performance, and security of your embedded systems, ensuring they meet the highest standards. We’re offering a free demo of T-Plan so you can see how it will help you improve your embedded system testing, which you can check out at the link below.